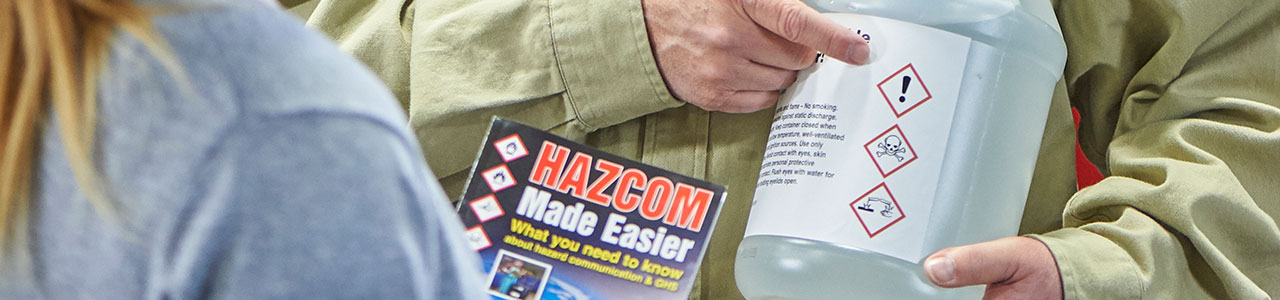
Hazard Communication (HazCom)
The OSHA Hazard Communication Standard (HCS), 29 CFR 1910.1200, is designed to protect employees from hazardous chemicals used or stored in the workplace. It gives workers the right to know and understand the chemicals they are exposed to and how to work with them safely. The standard aligns with the Globally Harmonized System of Chemical Classification and Labeling (GHS) for a consistent approach to classifying chemicals and communicating the hazards associated with their use.
Under the HazCom standard, all workplaces that have hazardous chemicals are required to maintain a chemical inventory and have a written hazard communication program. Laboratories and work operations where employees only handle chemicals in sealed containers, such as a warehouse, are not required to have a written program; however, they do have other responsibilities under the HazCom standard.
The written program must describe how it will meet the HCS requirements for: labels and other forms of warning for hazardous chemical containers, safety data sheets (SDS) for all hazardous chemicals, and training and information for any employee who has the potential of being exposed to a hazardous chemical
It also must include: a list/inventory of the hazardous chemicals present in the workplace, how the employer will inform employees of the hazards of non-routine tasks and the hazards associated with chemicals in unlabeled pipes, and how chemical hazard information will be communicated on multi-employer worksites